Rapid Prototyping

Fast, seamless, intelligent prototyping for your electronic products
Every new electronic product needs to be tried and tested before being launched to market. Rapid prototyping is the quickest and most seamless way to reduce the speed to ramp, while maintaining product quality and lowering costs. Product and circuitry tests conducted early in the manufacturing process are not only better for our customers, but mean that products can be modified quicker and out to market faster.
Why rapid prototyping is needed
In electronic manufacturing, a methodical, design-based approach is essential, as complex components and processes must be handled with skill, to ensure products are both efficient and profitable. Therefore, it’s vitally important that they are thoroughly tested at the prototyping stage to ensure excellent performance.
Software development is often delayed until a working hardware platform becomes available, so the prototypes are needed beforehand. Our rapid prototyping doesn’t just benefit customers who need a working version of their Printed Circuit Board Assembly (PCBA) to validate that the circuits function perfectly; it also shows design teams that the circuits fit into the size and space required, which then can be vigorously tested. And our prototyping goes beyond PCBs, as we prototype entire complex multi-level system products for our customers, including racks and cabinets.
It’s important to trial and test product design before progressing into mass production, because if anything is not compliant with requirements, then a re-design can unexpectedly become necessary delaying the product’s release to market.
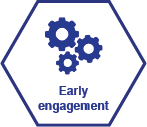
Early engagement in circuit design – With our New Product Introduction (NPI) team, we work closely with OEM design teams to ensure products are made with long-term efficiency and with life and cost-reduction in mind when the design is still fluid.
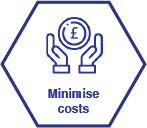
Avoiding wastage and minimising costs – We advise only optimal batch sizes, based on what’s best for each customer’s requirements. We supply components from our own stock, and with over 50,000+ part lines, there’s no limit to catalogue availability – which can help with cost effectiveness.
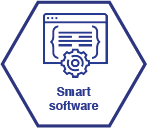
Smart software that sets us apart from our competitors – We rapidly establish baseline costs through our custom-developed, innovative programme which takes a customer’s bill of materials, compares this against our in-house stock base and then filters this out via APIs to various distributor networks.
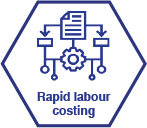
Sophisticated labour estimate algorithms – Allows us to generate accurate and rapid labour costing based on the construction of specific items, to stay on top of progress and ensure estimates are realistic and sustainable.
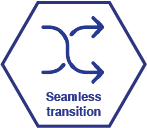
Seamless transition – The equipment we use for prototyping is the same that will be used for volume production. This helps us to check the product’s readiness, ensuring a smooth transition to large scale manufacturing. We believe in speed and not haste, so although we get your product to market within short timeframes, we never cut corners in terms of process, measurement or quality.
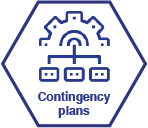
Built-in attrition and contingency plans – If anything goes wrong, wherever possible, our built-in attrition and contingency plans mean we can monitor progress and still deliver the full amount requested.
Looking for world-class electronic manufacturing services?
We help our OEM customers to reduce their time to market and simplify their supply chain.